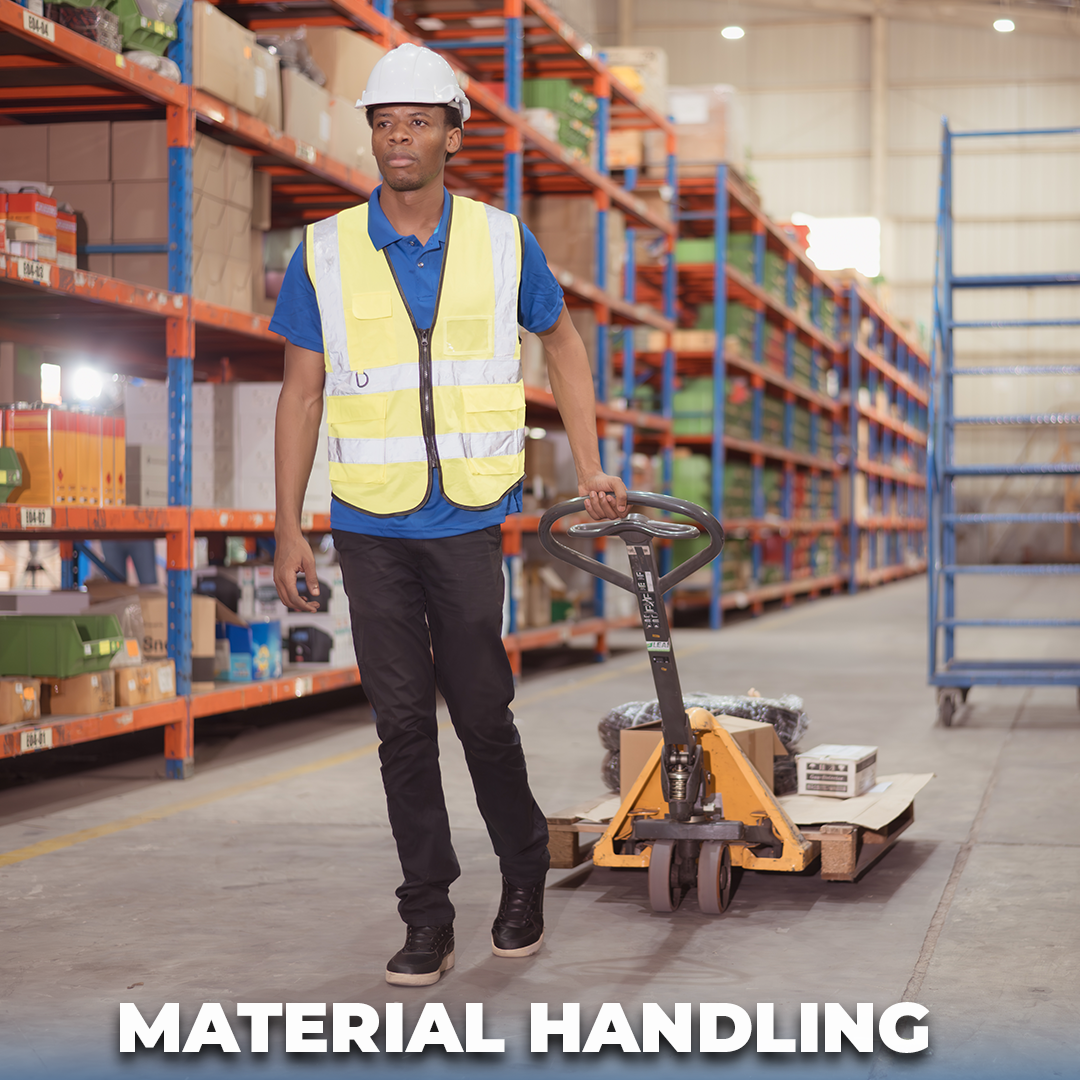
In today’s fast-paced industrial landscape, material handling plays a crucial role in ensuring efficient operations, safety, and cost-effectiveness. Whether in warehouses, manufacturing plants, or distribution centers, the methods by which materials are moved, stored, and controlled directly impact productivity and operational excellence. In this comprehensive guide, we will explore the three primary types of material handling—manual, mechanized, and automated—examine the equipment used, and provide insights into selecting the best systems for your business. This article also delves into key aspects of material handling and provides valuable resources to help you understand its full scope. For an in-depth overview, check out this material handling guide.
In today’s fast-paced industrial landscape, material handling plays a crucial role in ensuring efficient operations, safety, and cost-effectiveness. Whether in warehouses, manufacturing plants, or distribution centers, the methods by which materials are moved, stored, and controlled directly impact productivity and operational excellence. In this comprehensive guide, we will explore the three primary types of material handling—manual, mechanized, and automated—examine the equipment used, and provide insights into selecting the best systems for your business. This article also delves into key aspects of material handling and provides valuable resources to help you understand its full scope. For an in-depth overview, check out this material handling guide.
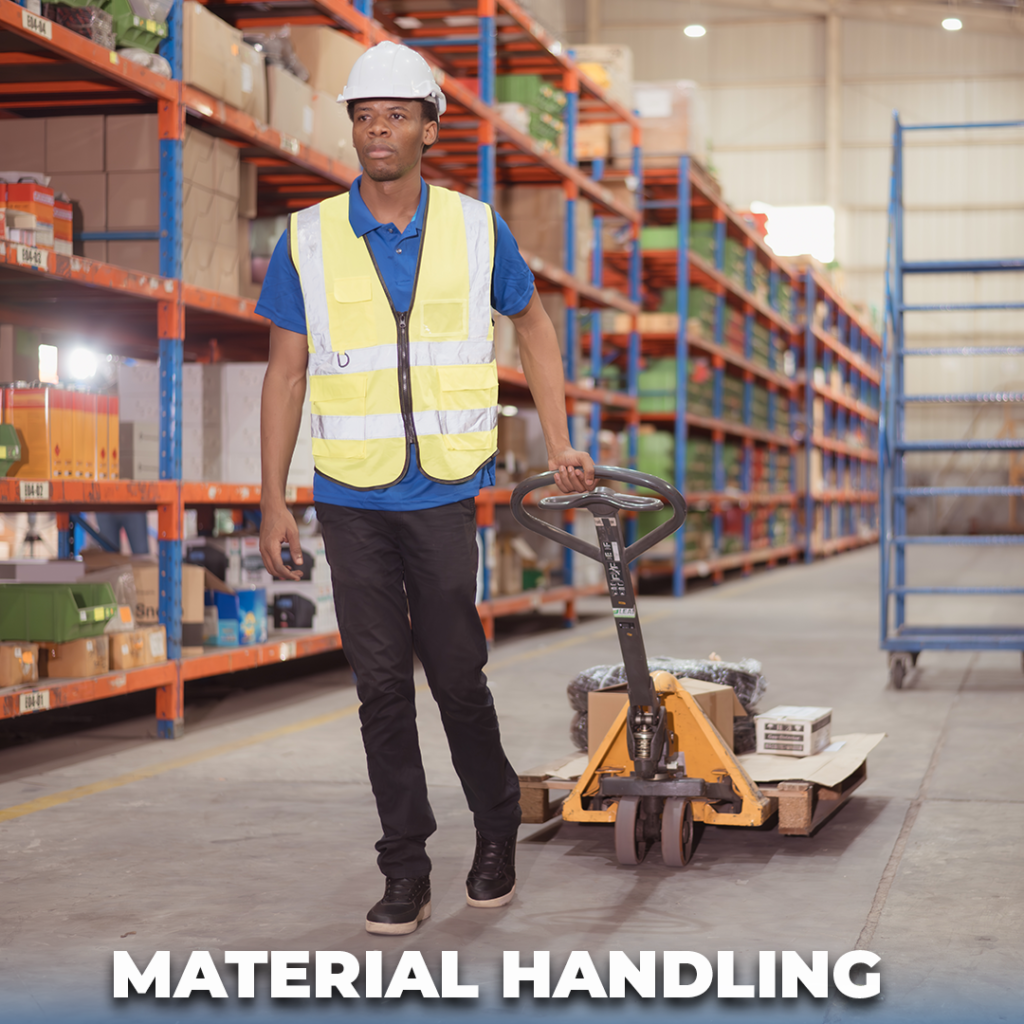
Introduction to Material Handling: Definition and Importance
Material handling is a term that refers to the movement, storage, protection, and control of materials throughout the process of manufacturing, warehousing, distribution, consumption, and disposal. A well-designed material handling system can transform operations by reducing labor costs, increasing productivity, and ensuring the safe handling of goods. Its significance can be understood by considering several key aspects:
- Efficiency: Streamlined processes reduce the time required to move products, ensuring a smoother production line.
- Safety: Proper handling techniques reduce workplace injuries and protect valuable materials.
- Cost Savings: Optimized material handling reduces product damage, minimizes waste, and cuts down on labor costs.
- Space Utilization: Effective storage solutions and equipment placement lead to better use of available space.
Understanding the material handling definition and its broad applications can help businesses of all sizes improve their operations while ensuring compliance with safety standards and operational protocols.
Material Handling Equipment: Essential Tools for Success
Modern material handling relies on a wide range of equipment designed to simplify the movement and storage of goods. Whether referred to as “material handling equipment” or “material-handling equipment,” these tools form the backbone of effective operations in industries such as warehousing, manufacturing, and logistics.
Material Handling Equipment vs. Material-handling Equipment
While the terms may appear similar, they both refer to the tools and machines used to handle goods and materials. Equipment can range from simple manual tools, like pallet jacks, to sophisticated systems such as automated guided vehicles (AGVs) and robotics. Each type of equipment is selected based on factors like the size and weight of the materials, the operational environment, and the specific handling needs of a business.
Investing in the right material handling equipment not only enhances operational efficiency but also improves safety and reduces long-term operational costs. Businesses are encouraged to explore detailed resources like this comprehensive material handling guide for further insights into equipment selection and industry trends.
The Three Types of Material Handling Systems
Understanding the different approaches to material handling is essential when planning or upgrading operational systems. Generally, these systems fall into three categories: manual, mechanized, and automated. Each type has its unique advantages and applications, which are detailed below.
Manual Material Handling: The Foundation of Operations
Manual material handling involves using human physical effort to move, lift, or store items. This approach is typically seen in smaller operations or in situations where the volume or nature of the goods does not justify the investment in mechanized or automated systems.
Advantages of Manual Material Handling
- Flexibility: Workers can easily adapt to various tasks and navigate spaces where machinery might be impractical.
- Low Cost: It requires minimal initial investment since there is no need for expensive machinery.
- Simplicity: Manual methods are straightforward to implement and often require little to no specialized training.
Challenges of Manual Material Handling
- Labor Intensive: Repeated manual lifting and moving can lead to physical strain, increasing the risk of injury.
- Lower Productivity: Human performance may vary, leading to slower processing times compared to mechanized systems.
- Inconsistency: Fatigue and human error can result in inconsistent performance and potential damage to materials.
Despite its limitations, manual material handling remains essential in environments where flexibility and low cost are priorities. Proper training and ergonomic solutions can mitigate many of the risks associated with manual handling.
Mechanized Material Handling: Bridging Human Effort and Automation
Mechanized material handling utilizes machines and powered equipment to assist in moving and managing materials. This category serves as an intermediary step between manual handling and full automation, combining the adaptability of human intervention with the efficiency of machinery.
Key Features of Mechanized Material Handling
- Enhanced Efficiency: Machines like forklifts, pallet jacks, and conveyor belts can move heavy items more quickly and consistently than manual labor.
- Improved Safety: Mechanized systems reduce the physical strain on workers, lowering the risk of injuries and repetitive stress disorders.
- Cost-Effective Over Time: While the initial investment is higher than manual methods, mechanized systems often lead to long-term savings through improved productivity and reduced downtime.
For example, specialized equipment such as a lifting clamp can be used to secure and move heavy loads safely and efficiently. The integration of such tools into a mechanized material handling system ensures that goods are moved with precision, reducing the likelihood of damage and increasing overall throughput.
Applications of Mechanized Material Handling
Mechanized systems are particularly beneficial in warehouses, distribution centers, and manufacturing plants where the volume of goods demands faster, more reliable movement. Conveyor systems can quickly transport items across large areas, while forklifts handle bulky or heavy materials with ease. The choice of equipment is often determined by the specific needs of the operation, including space constraints, material characteristics, and budget considerations.
Automated Material Handling: The Future of Efficiency
Automated material handling represents the forefront of technological advancement in logistics and industrial operations. By leveraging robotics, artificial intelligence (AI), and advanced sensor technologies, automated systems can perform tasks with minimal human intervention, achieving high levels of precision and speed.
Benefits of Automated Material Handling
- High Productivity: Automated systems can operate continuously without the limitations of human fatigue, significantly boosting output.
- Consistency and Precision: Machines perform tasks with a high degree of accuracy, reducing errors and material damage.
- Cost Savings: Although the initial investment is substantial, automation leads to long-term cost reductions through improved efficiency and lower labor costs.
- Data-Driven Management: Automated systems often integrate with warehouse management software, enabling real-time monitoring, predictive maintenance, and performance analytics.
Real-World Applications of Automated Material Handling
In large-scale operations, automated systems are indispensable. Robotic arms can sort and package goods, while automated guided vehicles (AGVs) navigate complex warehouse layouts to transport items. Such systems are particularly valuable in high-volume e-commerce warehouses and modern manufacturing facilities where speed and accuracy are critical.
Automated material handling not only enhances operational efficiency but also allows businesses to scale up operations without a corresponding increase in labor. By reducing the reliance on manual labor, companies can focus on innovation and quality control, positioning themselves as leaders in a competitive market.
Material Handling Definition and Its Impact on Business Operations
The material handling definition extends beyond just moving goods—it encompasses the entire process of ensuring that products are stored, protected, and transported efficiently throughout the supply chain. This holistic approach has a significant impact on overall business performance. Key benefits include:
- Streamlined Processes: A well-integrated material handling system minimizes bottlenecks and accelerates production cycles.
- Enhanced Inventory Management: Accurate tracking and efficient storage methods reduce waste and improve stock control.
- Reduced Operational Costs: Optimized handling systems lead to lower labor expenses, fewer product damages, and minimized downtime.
- Improved Customer Satisfaction: Faster and more reliable material handling ensures timely deliveries and high-quality products, strengthening customer relationships.
For a comprehensive exploration of these benefits, it is helpful to review in-depth resources on material handling.
Choosing the Right Material Handling Equipment for Your Operations
Selecting the appropriate material handling equipment is a critical decision that can significantly influence productivity, safety, and overall efficiency. Here are some factors to consider when making your choice:
Factors to Consider in Equipment Selection
- Volume and Weight of Materials: The nature and weight of the items being handled will determine whether manual, mechanized, or automated solutions are most appropriate.
- Workplace Layout: The design of your facility, including aisle width, ceiling height, and floor surface, plays a vital role in determining which equipment can be effectively deployed.
- Budget Constraints: While manual handling has low upfront costs, mechanized and automated systems require significant investment. However, these systems often yield long-term savings through increased efficiency.
- Safety Considerations: Worker safety is paramount. Modern material handling equipment is designed with advanced safety features to reduce the risk of accidents and injuries.
- Future Scalability: Consider whether the equipment can adapt to growing operational demands. Systems that integrate easily with new technologies (such as IoT or AI) offer the flexibility needed for future expansion.
Integration and Customization
Customizing your material handling systems to fit your specific operational needs is often the best way to ensure efficiency. Companies may start with a combination of manual and mechanized systems and gradually integrate automation as volumes increase and processes stabilize. Working with equipment suppliers who understand the nuances of material handling can help tailor solutions that meet both current and future needs.
Emerging Trends and Innovations in Material Handling
The landscape of material handling is continuously evolving, driven by advancements in technology and the ever-changing demands of the global market. Several emerging trends are shaping the future of this essential industry:
Internet of Things (IoT) and Data Analytics
The integration of IoT in material handling enables real-time monitoring of equipment and inventory. Sensors and connected devices can track product movement, detect potential issues, and provide valuable data that can be used to optimize operations. With data analytics, companies can forecast maintenance needs, streamline workflows, and improve overall efficiency.
Robotics and Artificial Intelligence (AI)
Robotic automation is rapidly advancing, with AI playing a significant role in enhancing the capabilities of automated material handling systems. Robots can learn from operational data, adapt to changes, and perform tasks with unmatched precision. This technological synergy not only boosts productivity but also minimizes errors and ensures a high level of consistency in handling processes.
Energy Efficiency and Sustainability
Sustainable practices are becoming increasingly important in material handling. Modern equipment is designed to be energy-efficient, reducing the overall carbon footprint of operations. Innovations such as regenerative braking in forklifts and energy-saving sensors contribute to creating environmentally friendly and cost-effective handling systems.
Customization and Modularity
Flexibility in material handling systems is essential in today’s dynamic market. Modular designs that allow for quick reconfiguration and customization enable businesses to adapt to changing product lines, order volumes, and customer demands. This adaptability is particularly valuable in industries where seasonal fluctuations or market trends require rapid operational shifts.
The Future of Material Handling: Embracing Innovation
As the global market continues to evolve, the future of material handling will likely be defined by greater integration of smart technologies, enhanced safety protocols, and increased automation. Businesses that embrace these innovations are poised to gain a competitive advantage by improving operational efficiency, reducing costs, and creating safer work environments. The following points highlight key areas of development:
- Automation Expansion: As automation technology becomes more affordable and reliable, more businesses will adopt fully automated material handling systems to meet high-volume demands.
- Enhanced Connectivity: The convergence of IoT, cloud computing, and real-time data analytics will enable more intelligent and responsive material handling systems that can adapt on the fly.
- Worker Safety and Ergonomics: Continued focus on ergonomics and safety features will lead to the development of equipment that not only improves efficiency but also safeguards the well-being of employees.
- Integration with Supply Chain Management: The seamless integration of material handling systems with supply chain and inventory management software will lead to more synchronized operations and better decision-making based on real-time data.
Investing in modern material handling solutions today will help businesses stay ahead of the curve, ensuring they remain competitive in an increasingly automated and data-driven world.
Conclusion: Embracing the Three Types of Material Handling
In summary, understanding the three types of material handling—manual, mechanized, and automated—is essential for any business seeking to optimize its operations. Each approach offers unique benefits and challenges, and the best choice depends on factors such as material volume, budget, workspace layout, and safety requirements. From the simplicity and flexibility of manual handling to the efficiency of mechanized systems and the precision of automation, effective material handling is a cornerstone of modern industrial and logistics operations.
By investing in the right equipment and staying abreast of emerging trends like IoT, robotics, and AI, companies can build robust systems that not only improve current performance but also provide scalability for future growth. As businesses continue to evolve, the importance of a well-integrated material handling system cannot be overstated—it is key to reducing operational costs, enhancing safety, and driving overall efficiency.
For those looking to deepen their understanding, comprehensive resources are available. Explore this detailed material handling guide for further insights into the benefits and implementation of advanced material handling systems.
Embrace innovation in material handling and invest in solutions like the lifting clamp to transform your operations. With a strategic approach to equipment selection and system integration, your business can achieve new heights of productivity and safety in today’s competitive market.
Ultimately, whether you rely on manual methods, mechanized equipment, or fully automated systems, understanding and implementing effective material handling practices is the key to sustainable success. By continually optimizing these processes, companies can not only improve efficiency but also secure a competitive advantage in an ever-changing industrial landscape.
As you evaluate your current processes and consider upgrades, remember that the future of material handling lies in adaptability, innovation, and a commitment to excellence. With the right strategy and tools, you can create a safer, more efficient, and more profitable operation that meets the demands of today and tomorrow.
This comprehensive exploration of material handling provides you with actionable insights into the three primary types of systems available. Whether you are just starting out or looking to upgrade your existing processes, understanding these approaches is crucial. Embrace the evolution of material handling to drive efficiency, safety, and profitability in every aspect of your operations.